Industrial
Slide thru the tabs to see each floor system.
Epoxy Coatings
Broadcast Coating Systems
Epoxy Slurry
Troweled Epoxy/Urethane Mortar
Self-Leveling Urethane Mortar
Chemical Resistant/ Secondary Containment Coatings
Epoxy Coatings (14-30mils)
Coating Systems provide customers an economical aesthetic solution for obtaining a seamless, durable, easy maintenance finish. Coatings are thin mil, solid color, high gloss, smooth, resin rich, seamless, epoxy based floor coatings. General Service epoxy coatings demonstrate good chemical and abrasion resistance. Typically installed in light duty traffic areas. Epoxy Coating Systems produce an appealing, smooth surface texture that is easy to clean. Although Epoxy Coatings will seal off, improve the look of, and assist cleaning of concrete surfaces; thin mil coatings will not remove or dramatically hide divots, holes, or large surface imperfections themselves and can actually highlight such imperfections. Patching and hole filling can help remove the most noticeable imperfections, but for those desiring very smooth consistent finish a thicker system may be recommended. Orange peel/ stipple finishes & Anti-skid textures are optional. Generally a 2-3 coat system consisting of Epoxy primer and Epoxy Top coat(s).They can also be completed with Urethane Sealer for increased abrasion, chemical & UV resistance.
Advantages
- Lower maintenance and life cycle cost vs. tile, sheet goods, and carpet
- Durable, impermeable and seamless.
- Good chemical resistance
- Protects substrate from chemical or physical attack
- Low odor / low VOC.
- (Optional) Customized finish with Partial/Sporadic Flake broadcast & Urethane Sealer.
- Easily cleaned, maintained and a more sanitary work environment.
- Unlimited colors, no minimum required.
- Can use multiple colors to Identify walk paths, storage areas, emergency exits or products, or etc.
- (Optional) Integral cove, base and curbs
- (Optional) Urethane Sealer for increased abrasion, chemical, UV resistance
Where to Use
- Light duty manufacturing Areas.
- Animal care facilities.
- Correctional facilities.
- Animal laboratories & housing.
- Hallways, Walkways.
- Corridors and assembly areas.
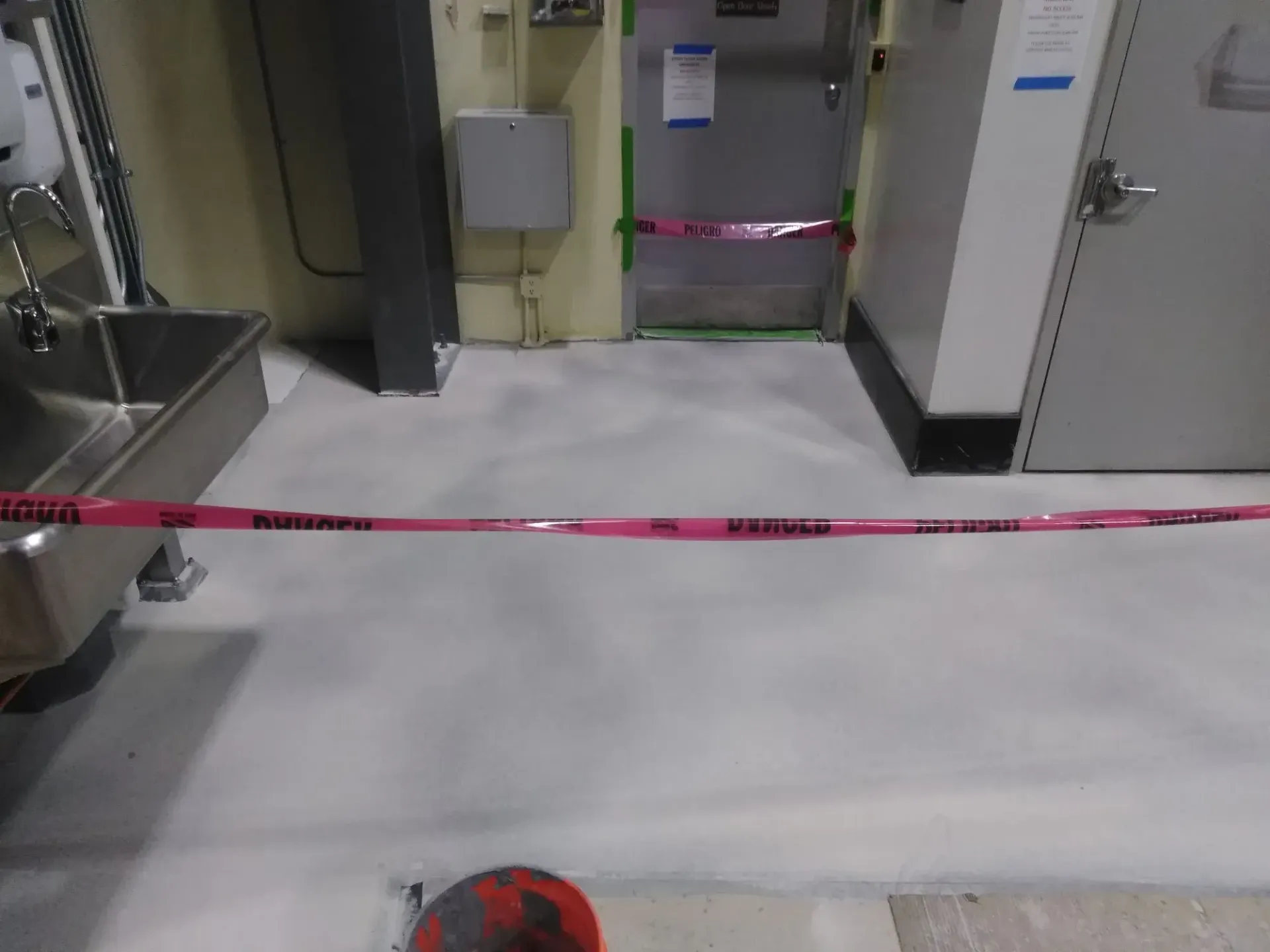
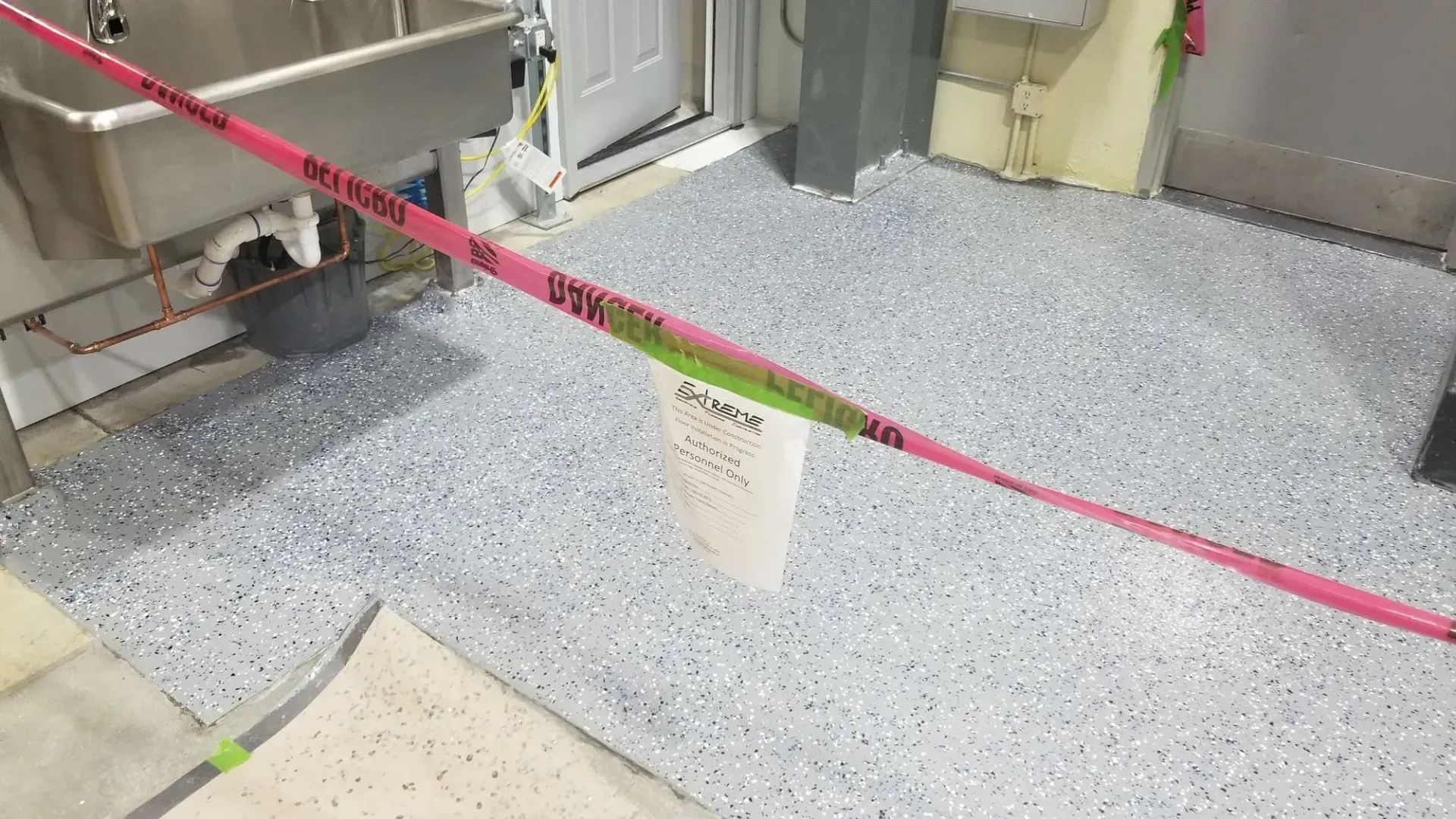
Broadcast Coating Systems (40-120 mils)
Broadcast Coating Systems are great solutions for light to medium duty environments. Broadcast coatings economically build system thickness, overall durability and performance of a coating by the incorporation of a hard aggregate broadcast layer that is sealed into the surface. The broadcast will dramatically improve a coatings life expectancy & resistance to wear, abrasion, and impact while also providing a chemical resistant and antiskid finish. Broadcast coatings are a solid color, textured, resin-rich, aggregate-filled, seamless, epoxy-based floor coating. Installed to protect new or existing concrete floors at a thickness range of 40 – 120 mils (1 – 3 mm). Broadcast System can be customized to meet aesthetic and slip resistance requirements. Generally 2-3 coat system consisting of epoxy/urethane primer, coating broadcasted to refusal, and top coat.
Advantages
- High abrasion and impact resistance.
- Good chemical resistance.
- Durable, impermeable and seamless.
- Variety of textures available
- Variety of slip-resistant surface profiles.
- Low odor / low VOC.
- Unlimited colors, no minimum required.
- (Optional) Urethane Sealer for increased abrasion, chemical, UV resistance
- (Optional) Integral cove, base and curbs
Where to Use
- Light duty manufacturing facilities.
- Animal laboratories & housing
- Locker & shower rooms
- Laundry rooms.
- Hallways, Walkways.
- Corridors and assembly areas.
- Interior slip resistant floor
Epoxy Slurry (70 – 160 mils (2 – 4 mm))
Epoxy Slurries provide some of the smoothest, slickest, rich colored, and easy to clean floors available. Self-Leveling Epoxy Slurries produce an aesthetic, smooth surface texture that is easy to clean and maintain. Epoxy Slurry Systems are solid color, smooth, resin rich, aggregate extended, seamless, epoxy based floor coatings. The incorporation of durable, fine aggregate into the matrix during mixing significantly increases the liquid resin volume during application without sacrificing physical properties and ultimately extend the coatings service life against aggressive wear. Due to the epoxy slurry properties nicks, scratches, and surface damage are less visible as the color is present throughout the entire matrix. Typically installed in light to heavy duty traffic areas, this general service epoxy coating demonstrates good chemical resistance as well as high abrasion and impact resistance. The system thickness is adjustable depending on condition of use. Slurries can generally fill and cover small divots, holes, and surface imperfections. Generally a 2 coat System consisting of an Epoxy Primer followed by an Epoxy Slurry Coat.
Advantages
- High compressive strength
- Good mechanical resistance.
- Good chemical resistance.
- Superior aesthetic finish.
- Durable, impermeable and seamless.
- Easily cleaned and maintained, resulting in a more sanitary work environment.
- Does not support growth of bacteria or fungus.
- Neutral odor.
- Unlimited colors, no minimum required.
- (Optional) Integral cove, base and curbs
- (Optional) Urethane Sealer for increased abrasion, chemical, UV resistance
Where to Use
- Cafeterias.
- Clean rooms.
- Convention centers.
- Institutional and recreational facilities.
- Laboratories and research facilities.
- Laundry rooms.
- Light to heavy duty manufacturing facilities.
- Packaging areas.
- Aircraft hangars
- Pharmaceutical facilities.
- Theaters and television studios.
Troweled Epoxy/Urethane Mortar (1/8”-1/4”) (3-6.4 mm)
Trowel Down mortars are commonly installed in environments with heavy traffic and higher potential for impact and abrasion. This heavy duty system is used to protect new surfaces or revitalize existing damaged, worn, and rough concrete. Troweled Mortar Systems are solid color, resin-rich, aggregate filled, seamless floor resurfacer. Troweled mortars completely resurface your current floor with a thickness of 1/8”- ¼” leaving you with a new flat, even surface with high density and compressive strength for exceptional durability. Can be used minimally in combination with other systems to patch large holes or damaged sections of concrete slabs. More durable than just a coating, a broadcast coating, or slurries; Troweled mortar systems deliver the highest performance for the toughest environments. Once the mortar has cured a variety of coatings & sealers can be used to meet a customer’s final surface aesthetic, appearance, and slip-resistance requirements. Final appearance will match that of a coating with the benefit of being smoother, more level, and flatter. This product is mixed in bulk mortar mixers, applied to the floor with screeds to ensure consistent application thickness and finished by hand troweling & power troweling. Once cured the floor is ground with planetary grinders to remove imperfections and trowel marks, then cleaned and coated.
Advantages
- Superior mechanical resistance
- High abrasion and impact resistance
- Good chemical resistance
- Durable, impermeable and seamless
- Easily cleaned, maintained and a more sanitary work environment
- Neutral odor
- Protects new concrete from abuse
- Rejuvenates worn surfaces
- Resists heavy traffic
- Reduced downtime
- (Optional) Slip resistant surface
- (Optional) Integral cove, base and curbs
- (Optional) Urethane Sealer for increased abrasion, chemical, UV resistance
Where to Use
- Dry processing areas
- Factories-light to heavy duty manufacturing areas
- High traffic aisles
- Laboratories
- Locker and shower rooms
- Health care facilities
- Beverage processing
- Urethane: Thermal Cycling/Shock Areas
- Animal care facilities
- Production lines
- Garage service bays
Self-Leveling Urethane Mortar (1/8”-1/4”) (3-6.4mm)
Commonly known as urethane cement, Self-leveling urethane mortars are used in medium to heavy duty environments. Particularly common in the food industry, commercial kitchens, areas with heavy water/liquid presence, and areas with thermal shock/cycling is a concern. Self-Leveling Urethane mortar is a solid color, three-component, water dispersed polyurethane-based/cement and aggregate screed. It is designed to provide excellent resistance to abrasion, impact, chemical attack and other physical aggression. Once laid self-Leveling Urethane is broadcast with aggregate to build thickness, increase surface texture and slip resistance and sealed with Epoxy, Novolacs, or urethanes. The system is typically installed at 3/16 to 1/4 in (4.5 to 6 mm) thickness. There are urethane cements used as moisture treatment solutions or non-food/pharma production areas that are installed at 125-160 mils. Urethane Cements are typically applied to concrete substrates or as resurfacing over previous urethane mortars.
Advantages
- Can be applied onto 7 to 10 day old concrete after adequate preparation
- Resists a very wide range of organic and inorganic acids, alkalis, amines, salts and solvents.
- Similar coefficient of thermal expansion to concrete allowing movement with the substrate through normal thermal cycling. It will perform and retain its physical characteristics through a wide temperature range
- Bond strength in excess of the tensile strength of concrete, concrete will fail first.
- Non-taint, odorless.
- Behaves plastically under impact / deforms but will not crack or debond.
- High abrasion qualities result from its aggregate structure.
- Extra Expansion joints are not necessary; simply maintain and extend existing expansion joints up through the Flooring System.
- Achieves highest performance ratings according to ASTM G21 resistance to fungi and ASTM D3273 resistance to mold growth.
Where to Use
- Areas With Thermal Cycling
- Areas with Thermal Shock
- Areas where Osmotic issues are present
- freezers & coolers,
- dairies,
- breweries, wineries, distilleries,
- laboratories,
- Commercial Kitchens,
- food processing plants,
- wet & dry process areas,
- chemical process plants,
- pulp and paper plants,
- Warehouses and storage areas.
- As Moisture Vapor Treatment
Chemical Resistant/ Secondary Containment Coatings (30-187 mils)
Chemical resistant coatings consisting of Novolacs and Vinyl Esters are used when floors & walls are exposed to harsh chemicals such as acids, bases, solvents, or oxidizers. These coatings are made to withstand exposure to the harshest chemicals and protect your substrate from chemical attack that erodes and destroys concrete substrates and foundations. Systems can be customized to include slurries, embedded fiber glass mat, broadcast, and mortars. The demands of each environment will determine the combination of systems or number of coats needed. Maintenance and cleaning are critical for these system to perform at the highest standards and areas that show wear or damage need to be addressed and fixed quickly to prevent the system from being compromised and leading to larger problems, failures, or potential containment breaches. We will work with you to develop and install a functional system as well as a maintenance and cleaning plan so your lining/ containment system performs as you need it to.
Advantages
- Customizable systems to meet environmental needs
- Protects Substrate From Harsh Chemicals
- Great for Horizontal or Vertical Surfaces
- High impact & abrasion resistance
- Can have textured anti slip finish
Where to Use
- Secondary containment
- Trench linings
- Truck unloading
- Battery charge stations
- Chemical production
- Chemical processing
- Chemical storage